A frost protected shallow foundation (FPSF) is an interesting and well-proven alternative to deeper, more-costly foundations in cold regions with seasonal ground freezing and the potential for frost heave - and the simplest way to build a solid and dependable foundation is to use frost protected shallow foundation (FPSF) forms - which come at a certain cost, but also with many advantages in terms of convenience, longevity and thermal performance - leading to a comfortable home with excellent energy efficiency and an efficient use of carbon intensive materials - like concrete.
The soil conditions of some building sites are simply not suitable for a slab-on-grade foundation with a thickened-edge footing without first beginning with extensive and costly soil remediation. Opting for a raft slab in such conditions can be a much cheaper option.
A raft slab is a type of frost-protected shallow foundation, or slab-on-grade foundation, that does not include the standard thickened-edge footing on which the entire load of the house bears. It is engineered to distribute the load evenly over the entire building surface.
Building sites with poor soil conditions (disturbed soil, expansive soils, low-bearing capacity, high water tables, etc.) traditionally require significant investment in drainage, soil replacement and compaction before an engineer will approve a project. Add the potential for frost heave in cold climates into the equation, and it's easy to understand why so many homebuilders and custom home construction companies tend to think they have to dig deep and install strip foundations below the frost line then deep frost walls. During a recent concept home build in Quebec, on expansive clay and with significant localized potential for frost heave - Ecohome chose instead to install a pre-engineered frost protected shallow foundation forms system.
The photos below are images of drainage measures that were required to support a thickened-edge footing slab-on-grade floor on a site with a high water table. Images courtesy of Yanni Milon.
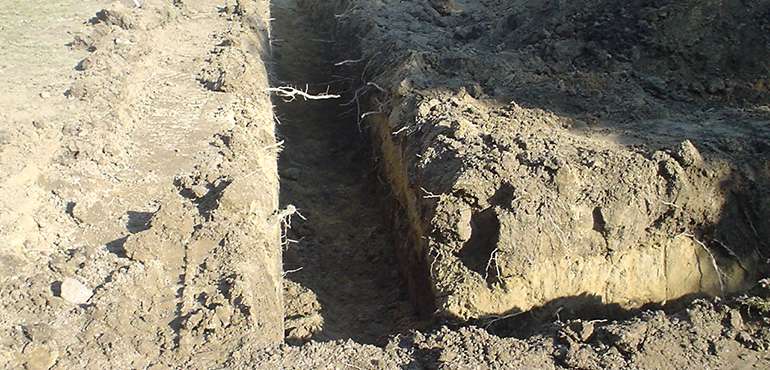
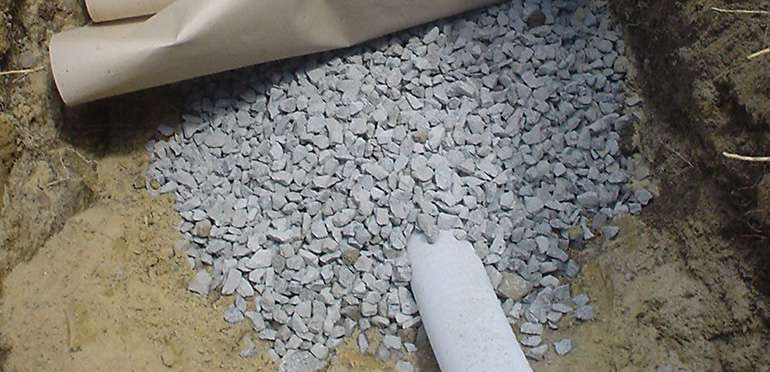
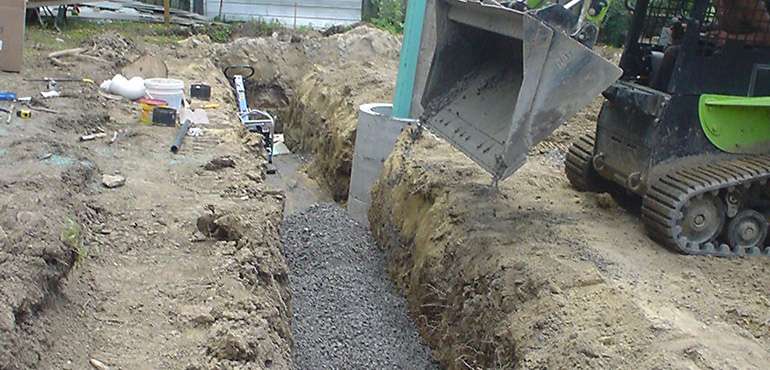
How do frost protected shallow foundations (FPSF) work ?
A FPSF raft slab acts a bit like a snowshoe in the way it distributes weight evenly over a larger surface. For this reason, they can often be built on soil that could not support other types of structures or ones subject to differential expansion and contraction, like expansive clay soils, or also frost heave in cold climates. In the case of our s1600 concept home, it was all of the above, so about as bad as it gets for designing, engineering and installing a succesful foundation system!
The typical soil bearing requirements for a thickened edge footing are 150 kpa (3,000psf), where a raft slab may be able to sit on soil with one third of that bearing capacity, or even less with additional engineering measures. This will often be the most affordable (and possibly only) option for building on sites with particularly unsuitable soil conditions. Even with an averaged-sized house, such costs can sometimes climb into the tens of thousands of dollars and possibly stop a building project in its tracks.
By choosing pre-engineered frost protected shallow foundations instead of going the traditional route for building foundations in a cold climate or on expansive clay soils, the risk of encountering inconsistently poor soil quality at the depth of traditional foundations is also avoided, so a raft slab on any site can avoid possible costly surprises once excavation has begun. Given its more robust design, it is also less prone to movement and cracking than buildings that bear on a footing as the whole foundation takes the load evenly.
You may or may not have success in finding an engineer experienced at this level of complexity in raft slab design, alternatively you can look into companies that specialize in custom designed prefabricated ICF slab on grade form kits, who also carry out all the engineering and can supply stamped drawings like we did.
Excavation and slab placement for cold climates
Our first recommendation, if at all possible, in constructing a frost protected shallow foundation at a reasonable cost is to choose a building lot that has a flat area sufficiently large to build the home you want to live in. Any leveling of the site, or digging in, creating a partially subterranean rear wall to the property adds a lot of additional complication, potential failure points, and most importantly time and expense. In general we find that the public or those who only build once or infrequently, underestimate the additional costs of building on a site that has changes in levels. After that, and having decided the optimal siting for insolation - especially if building to passive solar principles, here's a general timeline for building an insulated and frost protected slab-on-grade foundation.
- Remove the approximately 6 inches of organic material, two feet beyond where the building footprint will be.
- Build a retaining wall if necessary to create a level building surface.
- If there are large holes where tree roots have been removed, they can be filled with aggregate and compacted.
- If the site is sloped at all, bring it up to level with 0-2.5 inch compactable fill, being sure to compact it with a plate packer at the required intervals.
- Lay down 6 inches of levelled clean stone, two feet out from the building perimeter.
- Install pins where the corners of the building will be.
- Install all sub-slab plumbing, electrical conduits and radon gas evacuation tubes.
Note: We would strongly recommend seeking a plumber with experience in slab-on-grade foundation construction. As all plumbing work will be embedded in concrete, the accuracy of location, drain height and proper sloping of drains is essential.
- Install raft slab frost protected shallow foundation forms, interior floor insulation and reinforcement mesh as per engineering specifications.
- If you are installing in-floor radiant heating, be sure to have it designed by engineer to properly locate the heating delivery system so as not to affect the structural integrity of the slab.
Frost protected shallow foundation forms installation
First the formed edge pieces are laid in place, the corners need to be squared and secured in their location. following that is the installation of interior board insulation, a radon gas/vapour membrane, reinforcement mesh and any heating systems, all done according to the engineered building plans and directions. All slab images courtesy of Legalett.
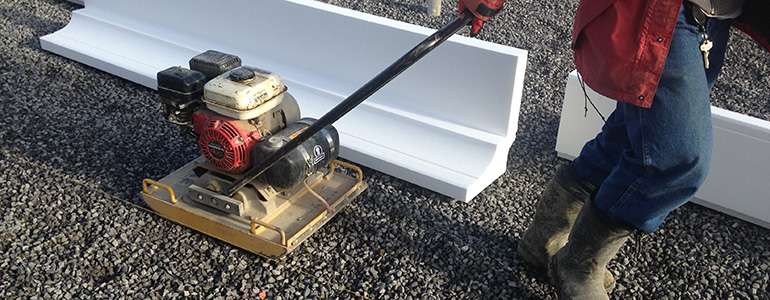
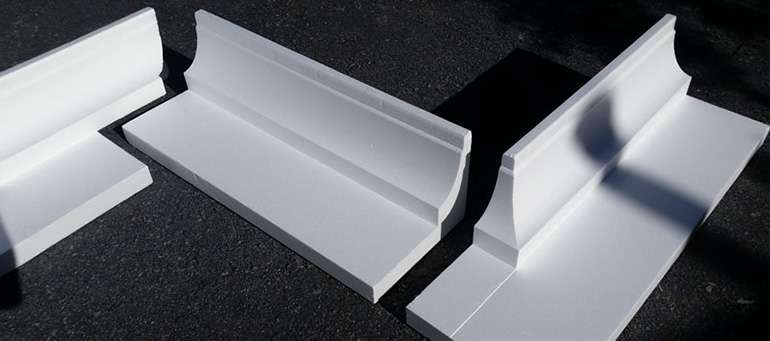

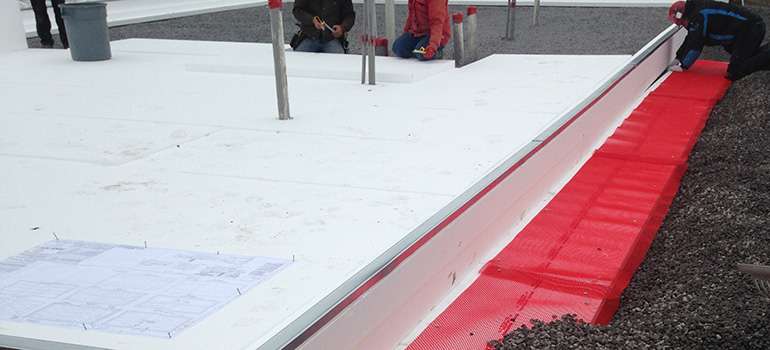
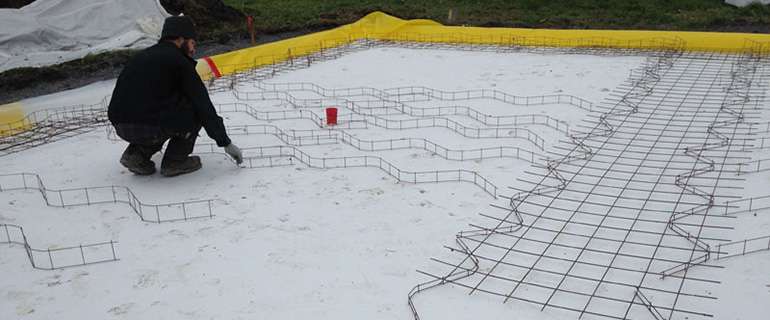
Slab-on-grade floors are often heated, which provides a very comfortable and even distribution of heat throughout a home. A large volume of heated concrete inside a building envelope will act as a thermal battery by storing and releasing heat, which helps balance temperatures in both summer and winter.
Such quantities of heated thermal mass inside the building envelope also provides heat security in the event of a power outage, by slowly releasing its heat over the course of days. Raft slabs can be heated with hydronic systems (liquid) or air-heated tubes as seen below.
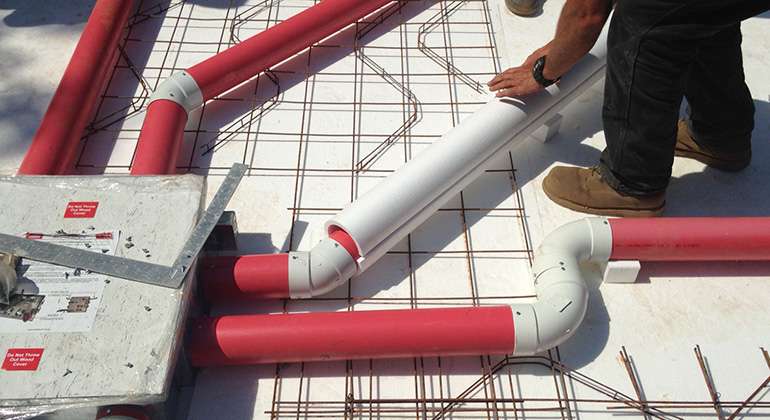
A better basement design - starting with an insulated foundation slab:
Traditional basements begin with a poured footing, then a foundation wall, and finally the slab floor. Rarely are footings insulated, and depending on how the walls are insulated, the result can be a thermal bridge between the footing and walls or floor. This brings unwanted heat loss, as well as a greater risk of condensation forming on those colder portions of concrete.
Alternatively, a basement can be constructed by beginning with a frost protected shallow foundation slab, followed by an ICF foundation wall. This provides a continuous layer of insulation separating the concrete from the ground. The result is a very comfortable and energy efficient basement, with no thermal bridging and reduced risk of mold.
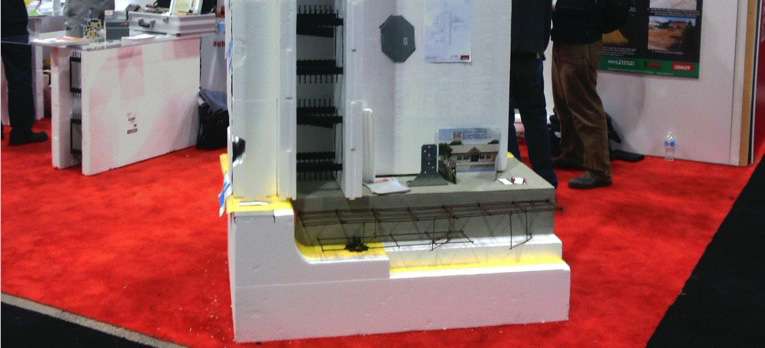
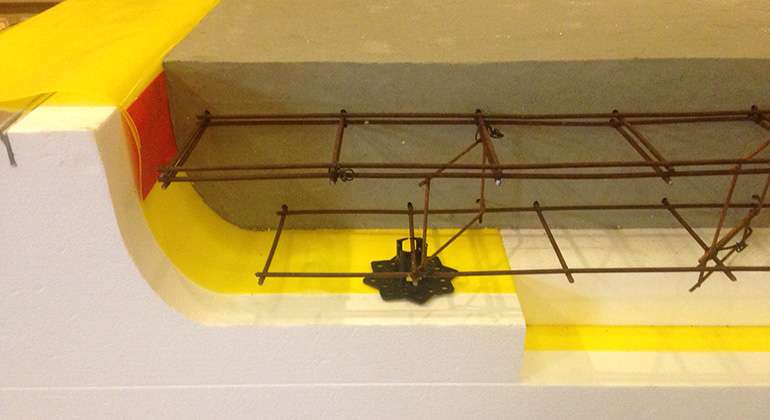
Hello. We have encountered a high water table and saturated soil in the area where we would like to build a garage with a loft/carriage house. We are wondering if an unheated raft slab is appropriate for the loads of a garage floor? Also, do you have any thoughts on using screw piles in lieu or in combination with a raft slab for this application?
Hi Rob, building on land with a high water table is exactly the place where a Legalett slab become advantageous as you don't need to excavate as deep when you aren't building a footing or frost wall. With this system you're only going down 6 inches to remove soil and you replace it with 6 inches (or more if needed) of clean crushed stone.
Screw piles work and may be a cheaper up-front solution but you would have higher heating and cooling bills as the underside is then exposed to ambient temperatures rather than the more balanced . There is also not a great resale value on houses built on helical piers. I can't speak to other slab solutions, but I know Legalett provides stamped engineering documents so all you need to do is provide them with your building plans and they take care of the rest.
I'm looking at building on flood fringe. The city requires that the main floor is 57" above grade. With neighbours on either side who have built prior to these bylaws (that have basements), how much of a perimeter do I need to hold that fill beneath the raft slab and create adequate drainage while keeping in mind the neighbours? What if anything needs to be done to protect against egress of fill during high water if fill is used to support just the house?
This site has been such an excellent resource. Keep up the great work!
Hi Meriah, glad you’re finding value in here, that’s always nice to hear. You would need to check with local building authorities for that in order to meet the set back requirements with adjacent lots. If for example any structures had to be 15 feet from the properly line (which it is where I live), that would likely apply to the foam skirting but not fill on top of it. There would probably also be regulations preventing you from draining water towards your neighbour, so that may affect the sloping and landscape design.
But typically speaking – you can raise the level of the slab base several feet simply by adding fill and compacting it at the appropriate intervals, and sloping it away from the house, which can be quite steep in necessary - you would just need to lay soil and a ground cover on top and it would be fine. The only issue is how close you are to the neighbour and how that sloping would impact them. Those are the general solutions, for the specifics on distance and sloping you would need to consult the house designer and local building inspector. Good luck, hope that helps!
Hi Mike, we are in the very early planning stages of our next home and durable, heated concrete floors are one of our most-wanted features. We are in a zone-7, low water table environment and your articles on ecohome.net regarding FPSFs have been extremely helpful. But I have a question: while cost is a major advantage with slab homes, a major limiting factor is storage without grade-level sq ft expansions, therefore is it possible to “marry” together a stick-built section (including a basement) with post-frame on a slab section? I know it would probably take some engineering, and maybe it’s a ridiculous premise in the first place, but it seems solving the storage dilemma with slab homes might open new market opportunities. Thanks again for the great articles !
Thank you Greg, we are always happy to hear when readers are finding articles of value. Doing a split level home is not a problem at all and is done all the time. It would add cost however, as you would be employing two different construction methods. You would need to build your bottom slab, pour foundation walls then do the upper slab, so it would mean at least 3 trips with a concrete truck, pump truck and crew (if not 5 or 6 depending on design) and that cost will add up quickly. That is an advantage of either a monoslab with footing poured at the same time or raft slab like above, it's one trip with expensive equipment.
It is true what you say that lacking a basement requires main level storage, but you may as well look at it from a perspective of expanding in one of two directions - down or outwards on the same level - and deciding which makes more sense for you. If you have limited room and cannot expand a slab enough to incorporate typical basement features such as a mechanical room and storage, then the cost of building a basement makes sense. If you have the ability to do so, expanding the main floor slab would be a cheaper alternative.
Slab designs will often marry together the mechanical room, storage, laundry, freezer, and even pantry it it's close to the kitchen, and it can be quite convenient compared to trips up and down stairs. So design it as you see fit, just remember the moisture challenges of basements and build sensibly if you go that route.